The Endless Battle with Gravity
TSE Barriers to Speed Part III of IV: Gravity (Weight)
What’s the first thing you do when someone shows you a carbon racing bike? Likely, you pick it up to see how light it feels. Zipp’s Total System Efficiency (TSE) approach to wheel design and the transition to a disc brake allowed our engineers to increase focus on reducing the weight of rims as a component of speed. In this Zipp Speed Podcast, Senior Design Engineer Ben Waite explains in detail how Zipp reduced the weight of wheelsets by hundreds of grams and how that influences performance. He discusses how you can now use specifications beyond rim depth and weight to select the best wheel. Below are edited excerpts from our conversation with Ben. For the full version, please listen to the podcast:
Listen to Ben discuss wheels and weight
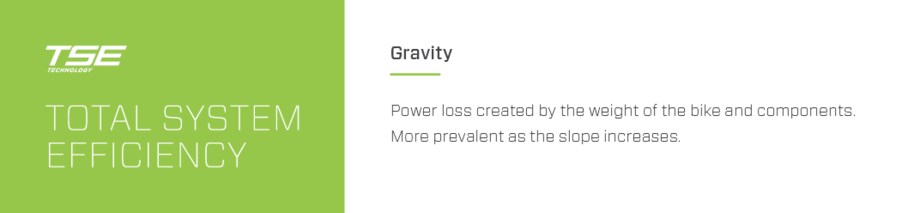
TSE Gravity
How did the current lineup of Zipp wheels (tubeless with hookless rim-tire interface) achieve significant weight reductions from previous models?
Going back over five years, we started with a “clean sheet” project—a clean sheet of how to make our rims. With rim-brake wheels, we tried to lead the way to be the first to have a carbon clincher that could withstand the temperatures from braking on the carbon braking surface. That was a massive project. But the requirements changed when we went to disc-brake road bikes. We no longer had to dissipate heat on the carbon braking surface. There were grumblings in the cycling industry that hookless might be a path forward. Just a few years ago, hookless and tubeless were rare things for road bikes. So, we started this clean sheet project; we could make a different rim. The advantages of going to a hookless design allowed us to design the wheels to be lightweight.
Zipp wheels are now hundreds of grams lighter than before. How does this change how riders evaluate the wheel model and rim depth best for them?
It changed from correlating mainly the rim depth with the type of riding (such as 404 for road racing, 303 for hills or gravel) to looking at other rim specifications. The internal width is one super-important part of the rim. Our 303 Firecrest and 353 NSW are 25mm internal width. That allows you to ride 30, 32, and 34mm wide tires. You move up the rim dept to 404s, 454s, 808s, and 858s; those are 23mm internal. A 28mm tire is going to fit nicely. But you also still want to think about weight. With the weight drop, you don’t have to think, “I can’t put a set of 858s on for a crit because they’re heavy.’ Now they’re about the weight of what a 404 used to be.
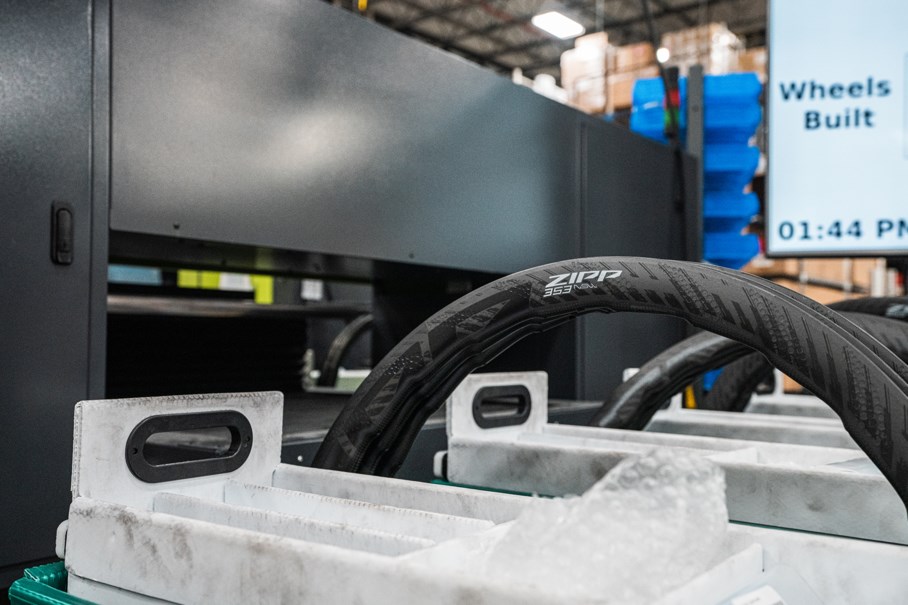
Zipp, for years, has said “aero trumps weight” when it comes to going faster—that aero efficiency is the most crucial consideration. How do gravity and the other barriers to speed (rolling resistance and vibration loss) fit into this approach?
Aero still trumps weight. But with TSE, weight still matters. There was this arms race to become as aero as possible, and people were adding weight. You go deeper or wider, whatever it may be. We’re still Zipp—we always go to the wind tunnel down the street. So, to separate ourselves, we focused on making our rims and dropping some weight.
Now you have a super aerodynamic wheel that, in addition, is lightweight for its depth.
–Ben Waite, Zipp Senior Design Engineer
Beyond using a scale to get weight, how do we test and verify Zipp wheels for weight and durability?
As we remove weight, we’re dialing into our impact testing. We’ve all been riding along and hit a big pothole, and that’s a jarring hit. We have an impact machine in the test lab. We hit the wheel with a weighted sled to see what it could withstand. There’s a UCI requirement, but we test a good bit beyond that. It’s wild being in the test lab. Seeing this hit to see a wheel system withstand some of those hits is impressive. It gives you confidence. (Also note our lifetime warranty covers Zipp wheels). Regarding durability, we have a machine that is a drum that rolls and applies a max rider weight and max lateral force. We have that longevity test that exerts force radially and laterally.