BOXXER DEVELOPMENT
Chassis Updates | DebonAir+ Twin Tube Design | Friction: Oil Flow Ports and Crown Height Gradient | Charger 3 and ButterCups | Great Things Take Time
Our BoXXer development story begins in Snowshoe, USA, at the final DH World Cup race of 2021—a double-header on Snowshoe’s rocky, rooty, rowdy track. With some early BoXXer prototypes in hand, a small crowd of development and testing engineers showed up in the pits atop Snowshoe Mountain and unloaded their test equipment into the SRAM trailer. The development team wasn’t there for the race but the testing event afterward—two days with the Trek Factory Race and RockShox Trek Race teams (and their mechanics) field-testing different iterations of BoXXer on the same track they had already raced twice. The goal: gather feedback from the world’s top downhill athletes on the new 38mm BoXXer. Armed with Data Acquisition (DAQ) setups, they set to work installing new athelete-specific BoXXer prototypes on frames, then set up the DAQ system on each bike to measure chassis bending and torsional movement, rigidity, vibration, and wheel speeds. (They also used this data to create RockShox’s newest Simulation Machine profile for lab testing, but that’s a story for another day.)
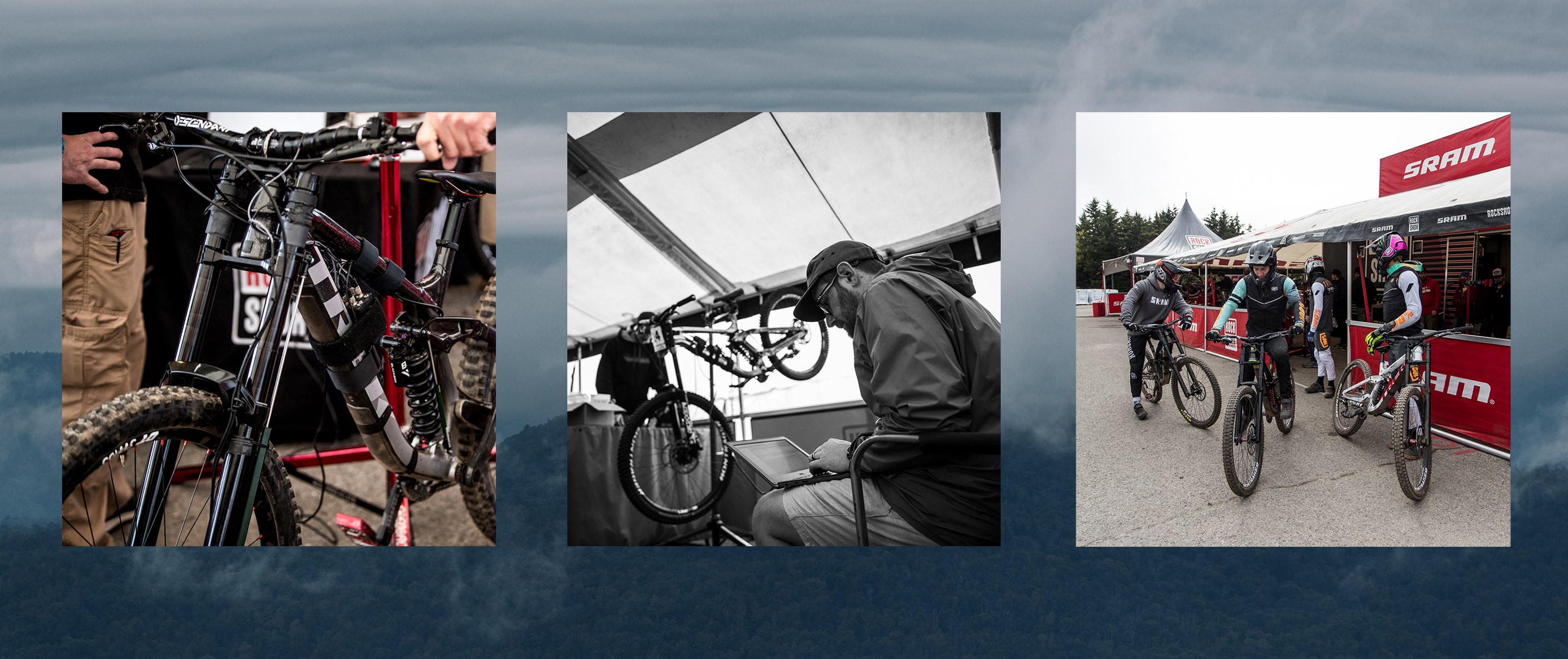
When the development team previously kicked off the new BoXXer project, they thought their new design was nearly baked. The 2023 lineup of technologies (developed by much of the same team) was well underway and getting great reviews, so they figured it would be a matter of dropping in ButterCups, the Charger 3 damper, and a model-specific version of the DebonAir+ spring into BoXXer’s longer chassis. But in addition to adapting those technologies for BoXXer’s use case, they knew they wanted to grow the chassis size to add stiffness. So that’s where they started: how stiff can we make it?
Spoiler alert: very stiff. Too stiff. (Yep, that’s a thing.)
Design Engineer Jon Watt and Product Manager Jon Cancellier were on site for the testing event, talking to the athletes after each run to get feedback. And what they heard was “too stiff,” repeatedly. Maybe not in those exact words, but disguised as “too harsh,” “searching for traction,” or simply “the small bumps are beating up my hands.”
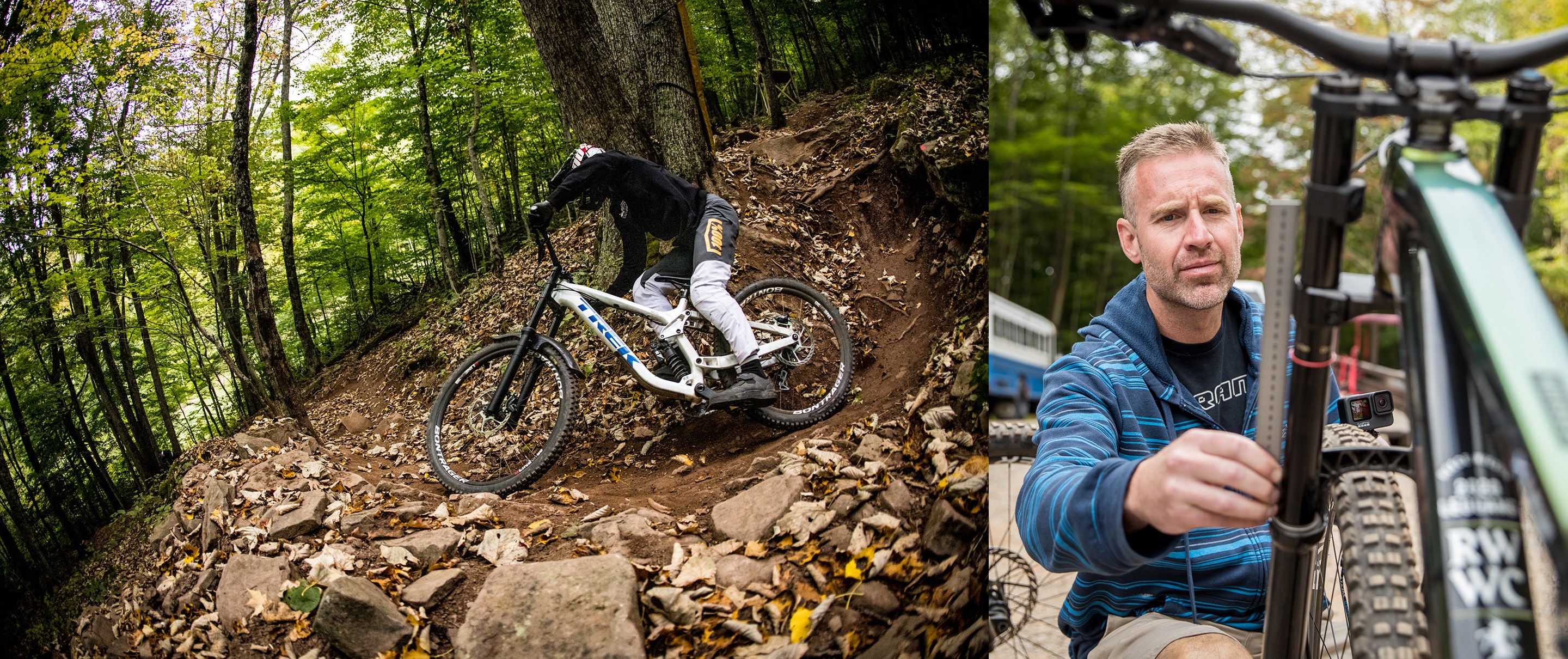
Other fork components can also be the cause of those comments, so how did the engineers know the chassis was too stiff instead of something else? It took some digging, but there were some key signs. When the fork has too much torsional or bending stiffness, it can dance away under the rider, deflecting off rocks and other obstacles, causing the rider to feel a loss of control and harshness in their hands. Too little stiffness and the fork feels like it’s tucking under the bike, or there are speed vibrations from the fork hitting its natural frequency, leading to uncontrolled feedback in the hands—ultimately, feeling unsupported during aggressive riding. When the fork has the *right* amount of stiffness, it can be more precise in holding a line—the fork meanders through rocks, absorbing small bumps so that the rider can focus on the track ahead.
Armed with the (admittedly not ideal) athlete feedback, the RockShox development team left the Snowshoe test event aggressively scratching their heads and spent the next 18 months redesigning every aspect of BoXXer.
We dug into that feedback—was it air spring, damper, or the chassis? We isolated each of those—for the chassis we would keep the same internals and try different stiffness, then do comparisons to see what they liked.
–Jon Watt
Chassis Updates
The first thing the team dug into was the chassis. The two main factors that affect chassis performance are torsional stiffness—how much the fork twists or resists twisting when an external force is applied (think side hits or rock gardens), and bending stiffness—how much the fork moves forward and backward beneath the bike (think applying the brakes quickly in a steep section).
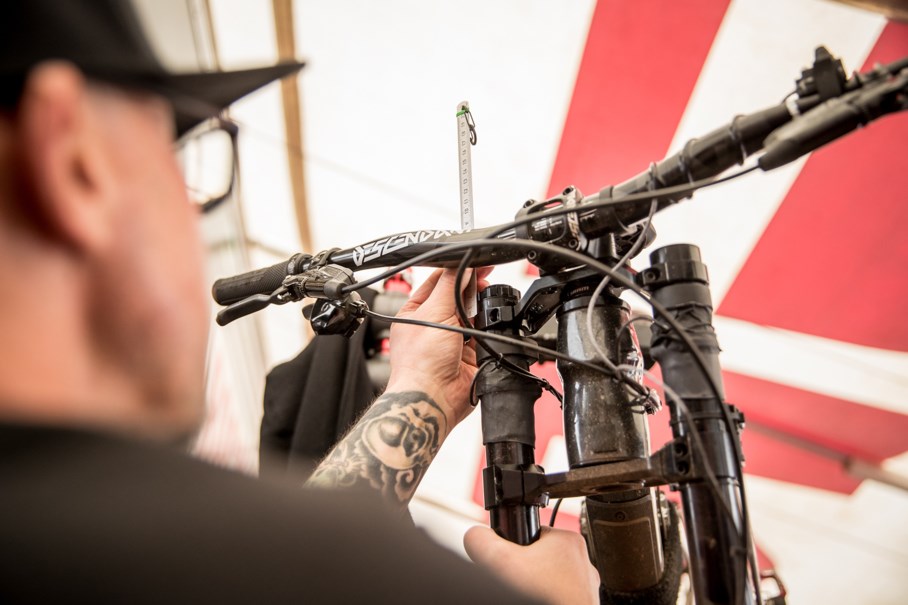
Bending stiffness is primarily determined by the upper tubes and crowns, which is why dual-crown forks are ideal for DH racers—they are markedly stiffer than single-crown forks. To combat the bending stiffness in BoXXer, RockShox Design Engineer Jon Watt got to work using Finite Element Analysis (FEA) to review stress points in the upper tubes, whittling down material and thinning out the wall thickness in critical areas for more flex where needed.
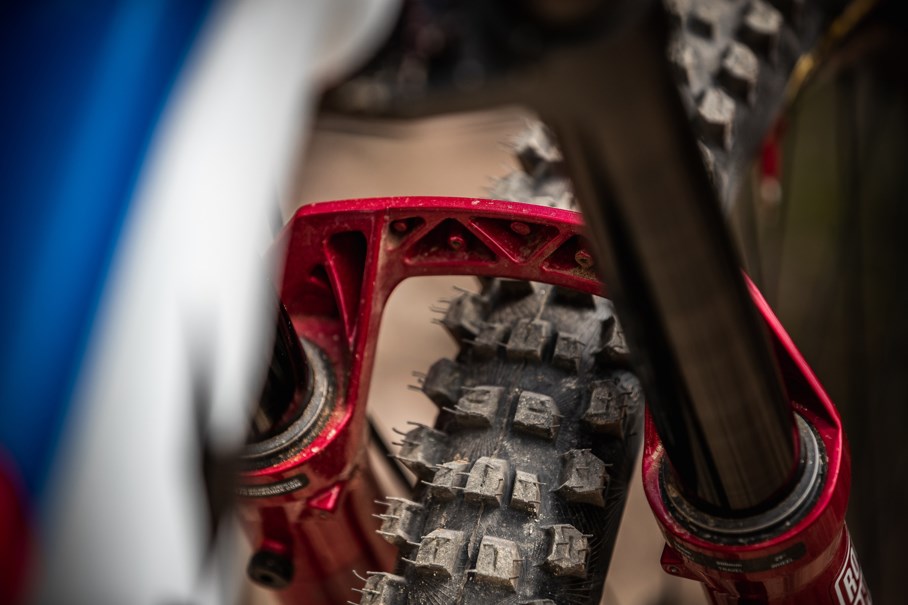
The perfect amount of torsional stiffness was a bit more challenging to nail down as the lower leg arch is the primary factor when looking at how the fork reacts to twisting forces. Lower legs are challenging to prototype because there are a lot of angles and curves that make it difficult to machine. To figure out how to reduce some of the torque on the brake arch, Watt began grinding material off some lower legs based on the FEA and stress analysis, ensuring that the testing provided a clear positive result before sending test riders out on the modified lowers.
I spent a lot of time running analyses to determine the best spot to take out material. It’s about optimizing strength to weight and stiffness to weight, putting material ONLY where we need it to keep it light while maintaining stability.
–Jon Watt
The team sent test riders out on one set of lower legs and then swapped them for another, and then another. They gathered feedback, adjusted the crowns, and sent them back out on test rides. Whittle, ride, measure, repeat. Eventually, things started coming together. The feedback from test riders was coming back positive, and the lab data reflected the same information—the Goldilocks chassis they were looking for was in sight.
Ultimately, the engineers landed on what they believe to be the perfect blend of torsional and bending stiffness, shown on the chart above in red compared to the stock 2019 BoXXer, the BoXXer athletes were racing in 2021, and the too-stiff prototype the athletes rode in Snowshoe on the far right.
DebonAir+ Twin Tube Design
As the chassis development was coming together, the team dove into restructuring the air spring. Growing the upper tubes from 35mm to 38mm impacted the air spring's feel and operation since the spring difference is pressurized within the upper tube. The first version of BoXXer's DebonAir+ air spring curve didn't produce the feeling they wanted—it was wallow-y and unsupportive in the middle of the stroke and ramped up too much at the end. The team was seeking a very linear, consistent air spring. With the larger upper tubes, however, they couldn't tweak the ratio between the piston and shaft diameters enough to make a linear curve, so the team considered a cartridge-style air spring to reduce that ratio.
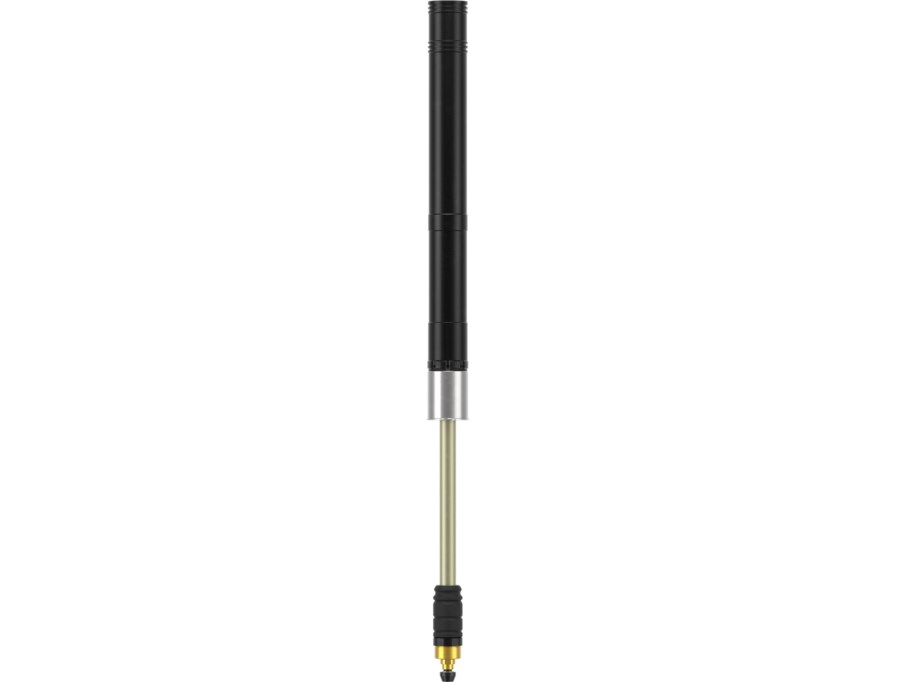
Enter the twin-tube design. By adding another tube within the upper tube, the team could decrease the piston diameter, reducing the ratio between the piston and air spring shaft diameters. They further reduced the ratio by growing the traditional 10mm air spring shaft to 14mm, and made it hollow to expand the negative chamber. With more ways to tweak the air spring volumes, the team bumped up the top of the air spring piston, similar to ZEB's air spring, and added a hollowed-out top cap to add as much negative volume as possible to achieve the ramp they were looking for. [Confused by all of this positive and negative air chamber talk? Check out DebonAir+ to learn more about air spring theory.]
Rounding out the updates to BoXXer’s DebonAir+ air spring, we added a 45mm-tall jounce bottom-out bumper to soften the blow during full-travel events. Similar to what you’d find in SID air springs, the jounce bumper engages at the bottom of the stroke as extra protection from the harshness of using all of your travel.
The result: a very linear, consistent air spring—easy to initiate travel for better small bump absorption, supportive enough through the middle of the stroke to prevent diving, and a relatively gradual end stroke so you can reach full travel, with the jounce bottom-out bumper to soften the blow when you do.
Friction: Oil Flow Ports and Crown Height Gradient
The next piece of the puzzle was friction.
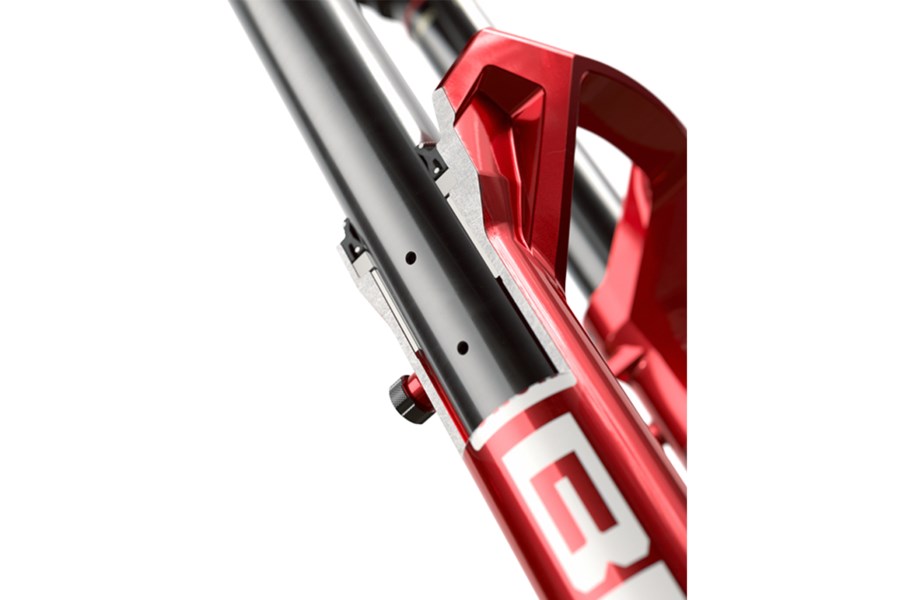
Designing the air spring into a cartridge opened up the opportunity to explore a theory they had about reducing friction from the system: if they added oil flow ports into the upper tubes, would friction decrease? The idea is simple: the drilled holes in the upper tubes (contained within the lower legs) capture lubrication at the bottom of the lower legs and release the lube through the lowers as the fork nears top out. The Oil Flow Ports keep the bushings lubricated—testing proved that this continuous oil circulation reduced friction overall. The Oil Flow Ports have a secondary purpose, though—they also give the air molecules that bounce around in the lower legs (known as casting volume) the opportunity to move through other parts of the internals without getting stuck… thus putting the finishing touches on BoXXer’s air spring curve.
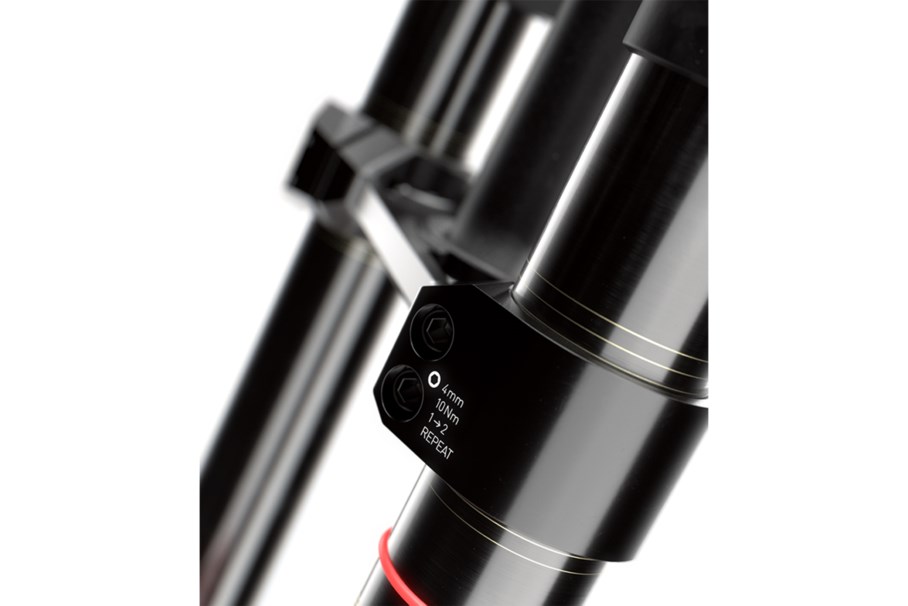
Another central point of friction is misalignment. For frame installation, BoXXer’s dual crowns require that the upper tubes are not connected as a one-piece CSU (Crown-Steerer-Upper) like most forks. Instead, the upper tubes must be aligned and torqued to spec in the crowns once the fork is installed on the bike—not from the factory. When the tubes are clamped into the crowns, they can skew slightly due to the force, pushing the tubes in one direction or another. However, due to BoXXer’s amount of travel, even minimal misalignment at the top increases once they enter the lower legs, and misalignment = friction. To combat that, we updated our crown design, added a new crown height gradient to help create a visual guide for easy alignment (eliminating any need for rulers), and created a new crown bolt tightening sequence to get the best alignment. Follow the instructions outlined in the BoXXer User Manual for the absolute best results.
Charger 3 and ButterCups
Finally, we added two of our technology heroes from the 2023 fork lineup launch: Charger 3 and ButterCups. Charger 3 RC2 (in the Ultimate model) features independent High and Low Speed Compression tunability, while the all-new Charger 3 RC (designed for the new BoXXer Base model) offers up Rebound and single Compression adjustability. Check out Charger 3 to learn more about how the damper works.
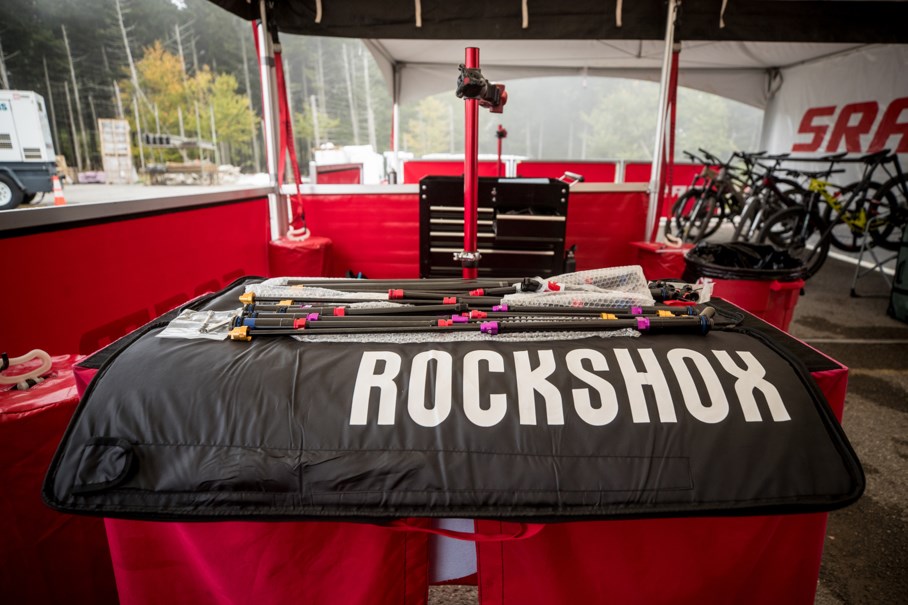
Prototype BoXXer Charger 3 dampers with ButterCups
The ButterCups you can’t live without from your 2023 Pike, Lyrik, and ZEB now also live on the damper and air spring shafts of Ultimate-level BoXXers. Inside their gold packaging, ButterCups utilize rubber pucks and a metal plate to absorb frequencies that would otherwise travel up to your hands and arms, preventing fatigue and soreness. Learn more about how ButterCups remove high frequency, low amplitude vibrations from your ride.
Great Things Take Time
BoXXer improved with every update we received, and it’s sick to see how it developed from our first ride on it.
–Vali Höll
Throughout the development process, through all the lab and field tests, athletes were racing iterations of BoXXer on local tracks and in the World Cup circuit. Before officially launching, Vali Höll secured five wins on the ’24 BoXXer, including snagging the 2022 World Champion title in Les Gets, France. Loris Vergier won two World Cup races on ’24 BoXXer, and scored a close third place at the same 2022 World Champs in Les Gets.
The key takeaway: great things take time. Sometimes, it takes hearing that you're on the wrong trajectory to reroute and find the right one.
We've changed so many things and figured so much more stuff out now as a result of failing. Had we nailed it the first time, we probably wouldn't have figured out all the other stuff that we did.
–Jon Cancellier
Check out Charger 3 Setup to guide you through the setup process for any Charger 3- equipped fork. Properly install your BoXXer using the instructions found in the BoXXer User Manual on www.rockshox.com. Questions about fitment? Head to the BoXXer FAQ page.
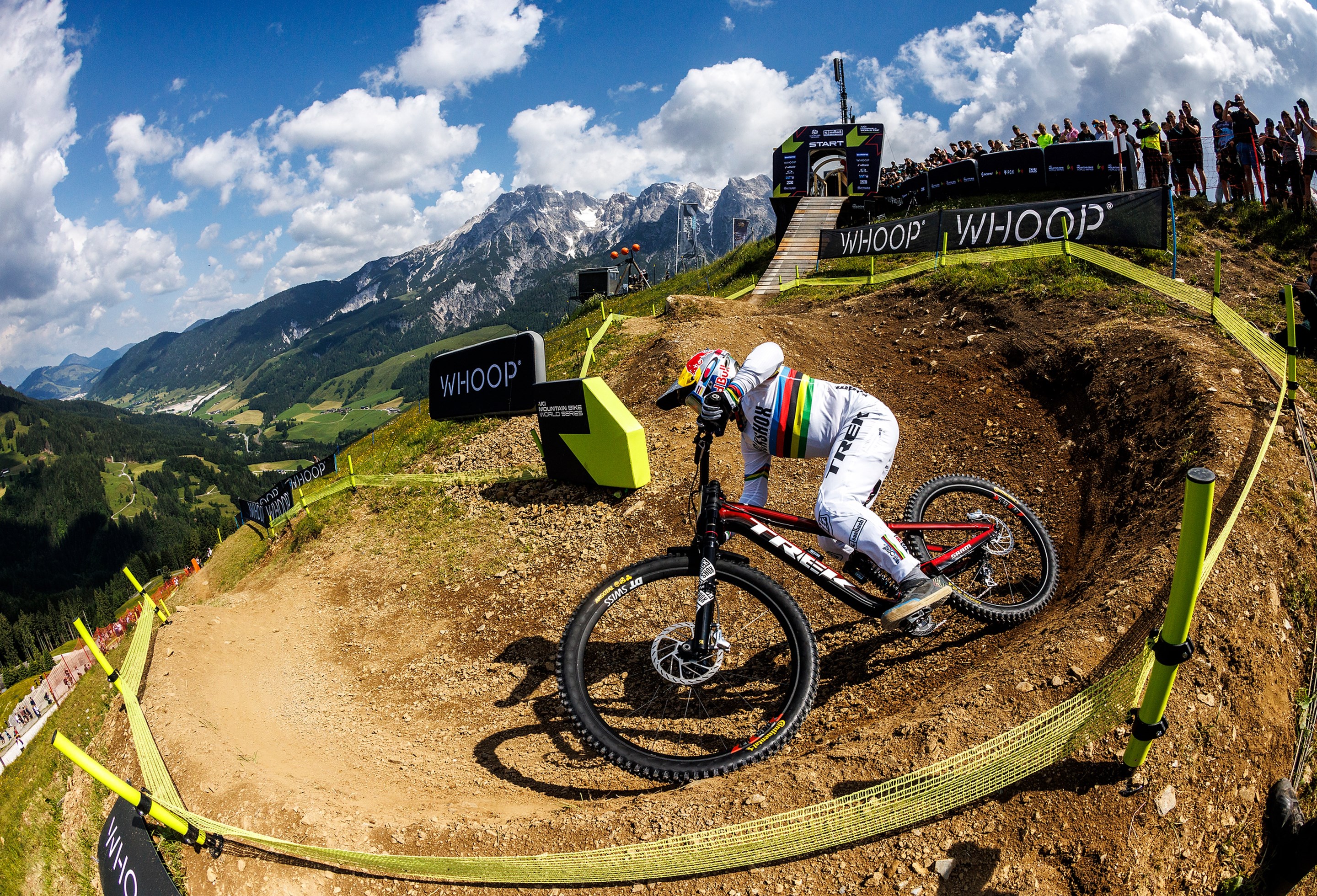
Photos by Andy Vathis. Words by Sarah Walter.